Die Entwicklung des Plattenharnisch begann im 15. Jahrhundert in Italien.
Die ökonomisch starke Stellung der mittel- und norditalienischen
Städte basierte auf einem hohen Entwicklungsstand von Handel und
Gewerbe. Die Städte waren zugleich auch die Mittelpunkte der Renaissance-Kultur.
In diesem für verschiedene Handwerke günstigen Klima konnte
sich auch das Handwerk der Plattner rasch entfalten. Mailand nahm hier
eine führende Stellung ein. Die berühmteste Werkstatt war die
der Plattnerfamilie Missaglia. Sie beschäftigte viele Fachleute,
hatte für ihre Aufträge eigens ein großes Handelsunternehmen
aufgebaut und ließ sich durch Agenten im Ausland vertreten.
In den deutschsprachigen Ländern entstanden insbesondere in Augsburg,
Landshut, Nürnberg, Innsbruck und Braunschweig ebenfalls Zentren
mit zahlreichen Plattnerwerkstätten. Annaberg wurde durch Peter von
Speyer bekannt. Plattner siedelten sich auch in anderen Orten an. Eine
Plattnergasse in Görlitz weist noch heute auf dieses Handwerk hin.
Die Plattner waren in Zünften organisiert. Plattnerordnungen regelten
die Herstellung und den Vertrieb der Waren. Die Zünfte schrieben
auch genau die Zahl der zu beschäftigenden Lehrlinge und Gesellen
vor. Amtliche Beschaumeister ließen nach Überprüfung der
Waffen und Rüstungsteile Beschaustempel als Qualitätszeichen
einschlagen. Jede Stadt hatte ihren eigenen Stempel, meistens in Form
des Stadtwappens. Beschau- und Meistermarken waren aber in den Plattnerordnungen
nicht immer vorgesehen. Viele Arbeiten lassen sich deshalb nur noch nach
stilkritischen Merkmalen geographisch und zeitlich einordnen. Wollte ein
Geselle die Meisterrechte erwerben, mußte er seine Arbeiten vor
einem Gremium angesehener Meister, den "Geschworenen" der Plattnerzunft,
vorlegen.
Nachrichten über die Herstellung von Harnischen sind äußerst
selten. Die Darstellungen von Hans Burgkmair im Weißkunig und die
Abbildungen im Hausbuch der Mendelschen Zwölfbrüderstiftung
in Nürnberg zeigen Waffenschmiede bei der Arbeit. In einem Holzschnitt
hat Hans Burgkmair den Besuch Kaiser Maximilians bei seinem Hofplattner
Konrad Seusenhofer festgehalten. Die Werkbank des Meisters ist mit Prelleisen,
Hämmer und kleinen Ambossen übersät (Kat.-Nr.
3).
Großschmieden verarbeiteten auf mit Wasser getriebenen Schmiedehämmern
das Roheisen zu Eisenplatten, die in diesem Zustand an die Harnischmachergeliefert
wurden. Die Weiterverarbeitung erfolgte per Hand und mit vielen an der
Schlagfläche gebogenen Treibhämmern, wie die auf der Innenseite
der Harnischteile sichtbaren Hammerspuren und Aufblätterungen beweisen.
Das Metall wurde zwar häufig ausgeglüht, die eigentliche Plattnerarbeiterfolgte
aber am erkalteten Metall, wie die Darstellungen von Burgkmair erkennen
lassen. Die Meister hämmerten alle Teile sorgfältig aus und
erhitzten die Teile mehrfach. So erreichten sie unterschiedliche Härtegrade,
denn nicht alle Teile wurden auf die gleiche Weise beansprucht. Viele
damit verbundene Feinheiten wurden als Werkstattgeheimnis sorgsam gehütet.
Anschließend wurden die Platten bearbeitet und poliert. Das erfolgte
an großen, mit Leder bezogenen Holzscheiben. Auch hier waren Spezialisten
tätig. Mitunter wurden die Harnische auch durch Einbrennen verschiedener
Ölmischungen geschwärzt, gebräunt oder durch Abschrecken
in Wasser gebläut. Dabei waren viele Farb-schattierungen möglich.
Im 16. Jahrhundert wurde die Ziertechnik der Ätzungen an Metallteilen
sehr beliebt. Dazu wurde die fertig polierte Oberfläche der Harnischteile
mit einem säurefesten Überzug aus Wachs, Öl und Asphaltlack
versehen. Es wurden zwei Hauptarten der Metallätzung angewandt: die
Tief- und die Hochätzung. Bei der zuerst genannten ritzte der Ätzmaler
mit einem Griffel eine Zeichnung in den Ätzgrund ein. Bei der Hochätzung
wurden die Flächen neben den Verzierungsmotiven weggeätzt und
der Grund häufig mit kleinen Punkten (Perlgrund) belebt. Danach wurde
der Ätzhintergrund häufig geschwärzt oder vergoldet, um
einen wirkungsvollen Kontrast zwischen den Verzierungen und den blanken
Metallflächen zu erzielen. Bei italienischen Arbeiten sind die Hintergründe
mit einer Kreuzschraffur ausgefüllt; deutsche Meister bevorzugten
die Punktierung.
Seit der Spätgotik beherrschten die Plattner ihr Handwerk virtuos,
als handelte es sich nicht um einen harten und schwierig zu bearbeitenden
Werkstoff. Erzielt wurden diese Leistungen durch über Generationen
hinweg gesammelte Erfahrungen und Fertigkeiten im Umgang mit diesem Material.
Die mit Hilfe von Hämmern auf kleinen Ambossen und Prelleisen hergestellten
kunstvollen Hohlplastiken und einfachen Maschinenmenschen bleiben unerreicht.
Ihre Herstellung würde heute den Einsatz einer hochkomplizierten
Technik erfordern.
Gerhard Quaas
|
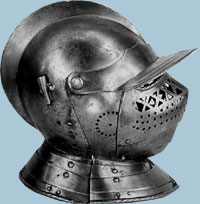 |